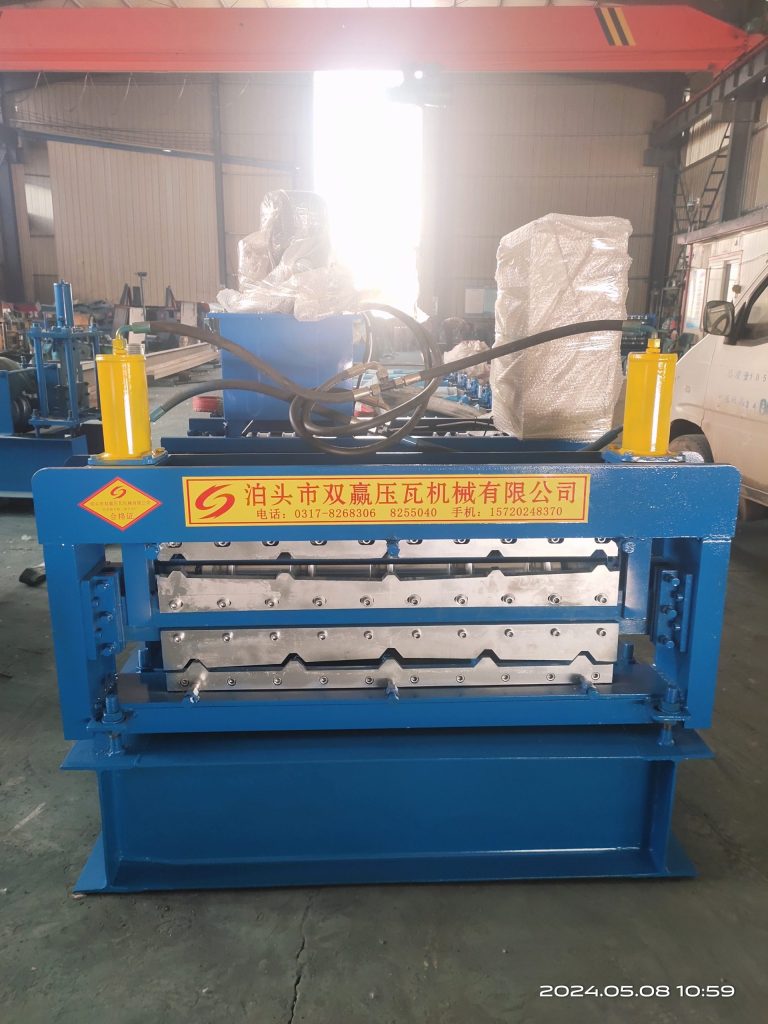
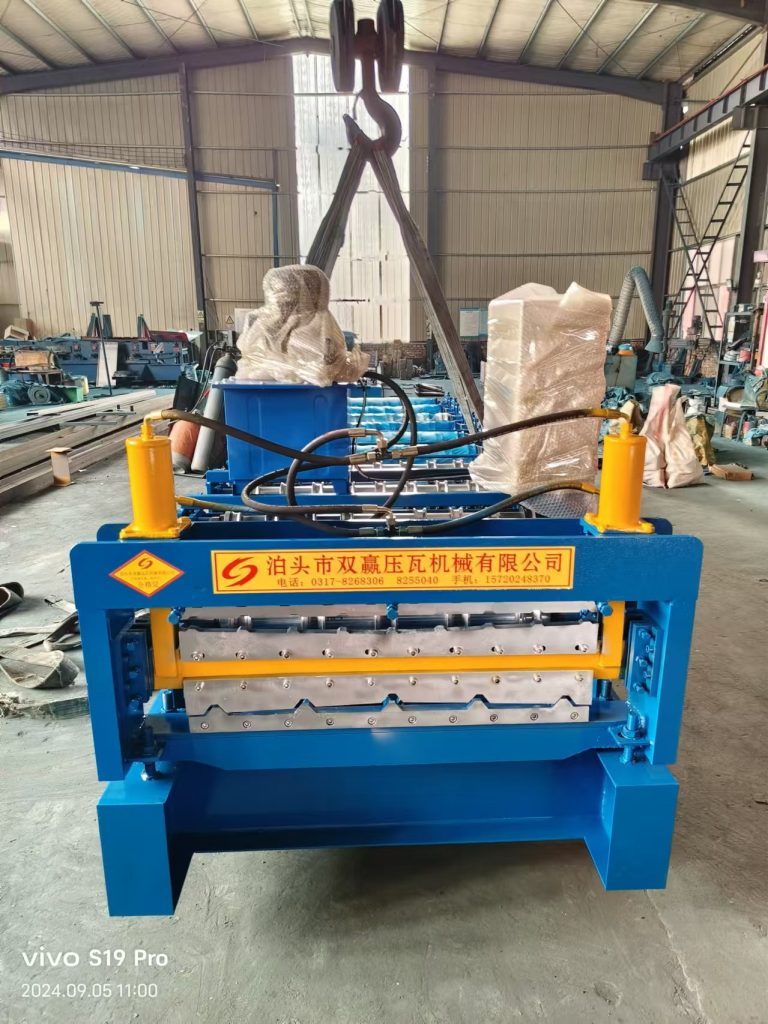
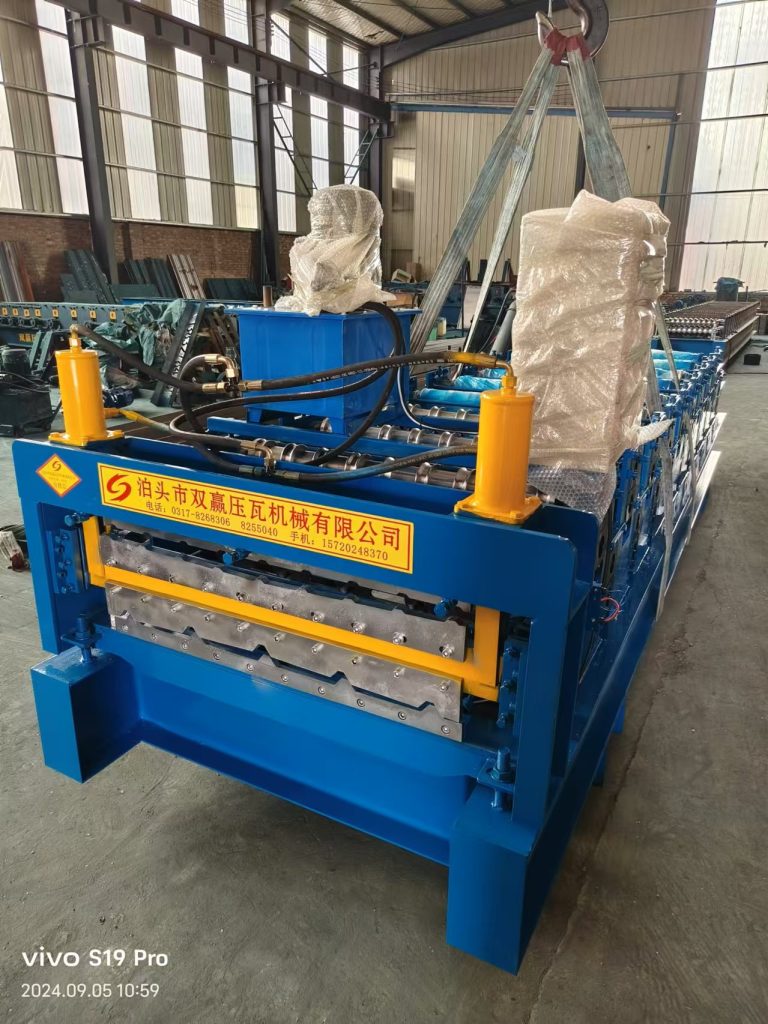
A Two-in-One Roll Forming Machine is a versatile piece of equipment designed to produce multiple types of roofing and wall panels from the same machine. This machine allows for the production of two different profiles, such as roofing panels and wall panels, using the same set of rollers, making it cost-effective and space-efficient for manufacturers. The ability to switch between profiles without changing the entire setup provides flexibility and increases production efficiency.
Two-in-One Roll Forming Machine
The Two-in-One Roll Forming Machine is a versatile and efficient solution for manufacturing both roofing and wall panels with a single machine. It is designed to accommodate the production of different profiles—such as roofing sheets and wall cladding panels—without the need to switch between separate machines. This dual-functionality not only saves space but also reduces equipment costs and increases production efficiency. It is an ideal choice for manufacturers seeking flexibility in their production lines.
Key Features and Functions:
- Dual Profile Capability:
- The Two-in-One machine can produce both roofing panels and wall panels using the same set of rollers. This allows manufacturers to create different products with one machine, making it a highly efficient choice for businesses that need versatility.
- Adjustable Roller Configuration:
- The machine is equipped with adjustable rollers, allowing for quick changes between different panel profiles. This flexibility ensures that the machine can easily switch between production of roofing and wall panels without complex reconfiguration.
- High Production Efficiency:
- The Two-in-One Roll Forming Machine is designed for high-speed, continuous production, offering high throughput while maintaining precision. The production speed typically ranges from 8 to 12 meters per minute depending on the material and profile.
- Material Flexibility:
- The machine can process a range of materials, including galvanized steel, pre-painted steel, and stainless steel. Material thickness can typically range from 0.3 mm to 1.0 mm, depending on the machine’s configuration and the required profile.
- Automated Control System:
- It is equipped with a PLC (Programmable Logic Controller) system that ensures smooth operation, easy profile adjustments, and precise control over production parameters. This automated system also enables high accuracy and easy operation for the operator.
- Integrated Cutting System:
- The machine features an integrated cutting mechanism, either hydraulic or mechanical, that ensures precise cutting of the panels to the desired lengths without distortion. The cutting is synchronized with the roll forming process to ensure consistency.
- Space and Cost Saving:
- By combining the functionality of two machines into one, the Two-in-One Roll Forming Machine saves valuable production space and reduces operational costs associated with maintaining multiple machines.
Performance Parameters:
- Material Thickness:
Typically 0.3 mm to 1.0 mm (depending on the material and profile type). - Panel Width:
Can vary, typically from 600 mm to 1250 mm, depending on the desired profile and machine configuration. - Production Speed:
Generally 8-12 meters per minute, depending on the material and complexity of the profile. - Rollers:
Number of rollers can range from 12 to 20, depending on the profile complexity. - Cutting Method:
Hydraulic or mechanical cutting, synchronized with the forming process for precise panel lengths. - Control System:
PLC (Programmable Logic Controller) for easy operation and profile switching. - Power Supply:
Typically 380V, 50Hz (adjustable depending on regional requirements). - Machine Dimensions and Weight:
The machine’s weight and size can vary based on its configuration, typically ranging from 5 to 10 tons.
Advantages of the Two-in-One Roll Forming Machine:
- Cost-Effective:
Produces both roofing and wall panels from a single machine, reducing capital investment and maintenance costs. - Space-Saving:
Combines the functionality of two machines into one compact unit, saving valuable factory space. - Versatility:
Ideal for companies that need flexibility in producing multiple types of panels for different construction projects. - Durability:
Built with high-quality components to ensure longevity and reliable performance under continuous production conditions. - Energy Efficient:
Designed to optimize energy consumption while delivering high production output.
Applications:
- Roofing:
Ideal for producing various types of steel roofing panels for both residential and commercial buildings. The roofing panels are known for their durability, weather resistance, and aesthetic appeal. - Wall Cladding:
Used to create wall panels for industrial, commercial, and residential buildings. The panels offer excellent insulation and protection from the elements, adding both functionality and design appeal.
Example Configuration:
- Material Thickness: 0.3 mm – 1.0 mm
- Panel Width: 1000 mm
- Production Speed: 10 meters/min
- Panel Length: Adjustable (typically up to 6 meters)
- Rollers: 16-18 rollers
- Cutting Method: Hydraulic cutting
- Power: 5.5-7.5 kW
Contact Us:
For more information or to request a quote, please contact:
- Whatsapp: +8613832784260
- Email: zhaohuabb@163.com
- Company: China Botou Win-Win Roll Forming Machine Co., Ltd.
Specification | Details |
---|---|
Product Name | Color Steel Tile Press Machine |
Brand | Win-Win |
Frame Material | 400H Steel |
Drive Power | 3-5.5 kW |
Transmission Method | Chain |
Chain Size | 1 inch – 1.2 inches |
Shaft Diameter | 70 mm |
Shaft Material | 45# Steel Tempered |
Wheel Material | 45# Steel Hardened Chrome |
Side Plate Thickness | 14 mm |
Hydraulic Power | 3-5.5 kW |
Hydraulic Method | Gear Pump |
Tile Output Speed | 8-12 meters per minute |
Feeding Width | 750-1250 mm |
Machine Dimensions (LWH) | 5000 x 1400 x 1200 mm |
Weight | 2-5 tons |
Unit Price | 8000-15000 USD |
Model | 820 Type, 840 Type,820type,900type,1000type |